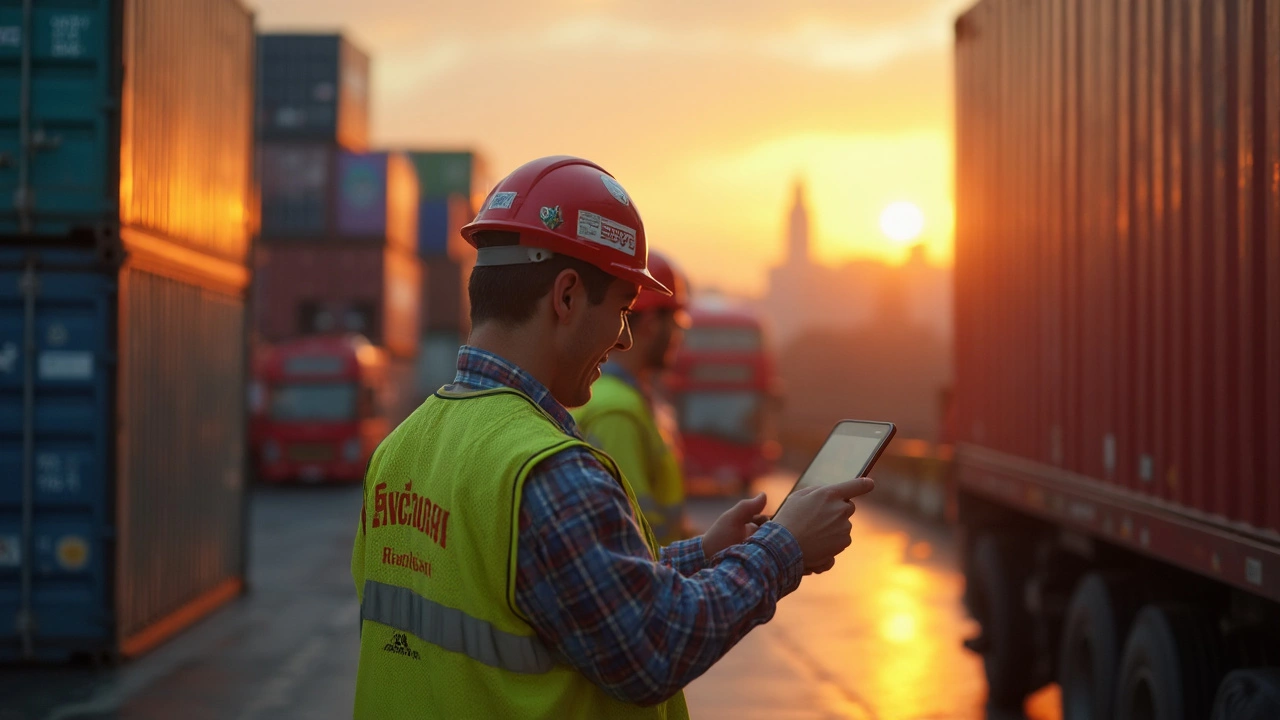
You might think logistics is just about moving stuff from A to B. It's a whole lot more, and yes, the stress levels can be intense. Picture trying to get medical supplies across the country in a snowstorm, or making sure that one lost package doesn't ruin someone's wedding day. Every minute counts.
The clock is always running, and you rarely leave work at the office. Phones buzz at dinner. An unexpected delay? You’re the fixer. If it goes wrong, everyone—from your boss to the end customer—lets you know. There’s no hiding in the backroom when a shipment is late.
But here's the thing: plenty of people love this pressure. They thrive on the challenge and the rush. The key is knowing how to manage that stress instead of letting it steamroll you. Stick around. I'll break down where the pressure comes from, why it happens, and some tricks from insiders who make it work—sometimes with nothing but quick thinking and a gallon of coffee.
- Running Against the Clock: Why Deadlines Matter
- Supply Chain Surprises: When Plans Get Tossed
- People Pressure: Handling Teams and Customers
- Technology Blues: More Gadgets, More Headaches?
- How Industry Vets Tame the Stress
- Can Logistics Ever Be Chill? Balancing Work and Life
Running Against the Clock: Why Deadlines Matter
In logistics companies, deadlines aren’t just suggestions—they’re the backbone of the entire operation. If you miss one, there's a domino effect. Trucks get stuck waiting, warehouses fill up, and customers start blowing up your phone. Everything, from a supermarket getting its milk in time to factories receiving vital parts, rides on these ticking clocks.
One fact I find wild: according to FreightWaves, nearly 70% of all freight in the U.S. moves by truck, and most operate on tight slots—sometimes down to 15-minute delivery windows. If a logistics company misses that, drivers can get fined or bumped to the end of the line, which just creates more stress down the chain. This isn’t just about packages—it’s about money, teamwork, and client trust on the line every single day.
Want to know how deadlines pile up? Here are the main ways they hit:
- Customers expect fast shipping. Thanks, Amazon Prime.
- Companies use just-in-time delivery to cut costs—meaning even a small delay can shut down a whole production line.
- Seasonal spikes, like holiday shopping, cram even more orders into tight timelines.
- Drivers and warehouse staff often work against the clock, facing overtime rules and government regulations about hours of service.
Common Deadline Pressures | Impact if Missed |
---|---|
Late port arrival | Expensive demurrage fees, missed export windows |
Missed truck loading slot | Rescheduling costs, angry customers |
Production delay | Factory idles staff, lost revenue |
Final mile disruption | Bad reviews, loss of client trust |
People who succeed in logistics develop ninja-level time management. Fast responses and creative thinking are non-negotiable. If you work here—or want to—you’ll need to get good at juggling these deadlines without dropping the ball (or your sanity).
Supply Chain Surprises: When Plans Get Tossed
If you’ve been in logistics for more than five minutes, you know nothing ever goes 100% according to plan. Maybe a truck gets a flat tire in rush hour traffic. Maybe a shipment disappears somewhere between customs and your warehouse. Or ports shut down because of a freak storm. Stuff happens, and usually at the worst possible time.
The global supply chain is like a set of dominoes. When one topples, the others can tumble fast. Look at early 2020: supply chain disruptions hit almost every industry when factories in Asia paused for lockdowns. One delayed container turned into empty store shelves halfway across the world. The issue isn’t just big crises either—small hiccups add up. According to a 2023 Gartner study, 72% of logistics companies said they deal with unexpected supply chain issues every single week.
What makes these surprises so stressful? Here’s a quick rundown:
- Timing is critical. One late delivery can throw off production lines, retail launches, and even healthcare schedules.
- Visibility is limited. You don’t always know exactly where shipments are or when problems will pop up.
- Customer expectations keep rising. Thanks to online shopping, people expect real-time tracking and nearly instant deliveries.
Every adjustment sets off a scramble. You're making calls to reroute trucks, bargaining with freight companies, and updating dozens of people. Sometimes you have five backup plans—and still have to invent Plan F on the fly. People who thrive in logistics companies tend to expect the unexpected. They also build relationships with vendors and partners so they’re not starting from scratch when things blow up.
Got some downtime? Build a crisis checklist. Here’s what experienced folks do:
- Keep a contact list of backup carriers and suppliers.
- Automate tracking and alerts so you spot problems sooner.
- Keep customers in the loop—people get less mad when they’re updated honestly.
- Document every mistake so next time, your team reacts faster (or avoids the same potholes).
Roll with the punches, but plan for the chaos. It’s not just about surviving surprises—it’s about turning them into a win for the whole operation.
People Pressure: Handling Teams and Customers
If you ask anyone working in logistics companies, they'll tell you: people pressure is real. It's not just about moving goods—it's about keeping the peace between warehouse teams, delivery drivers, and customers who want everything yesterday.
It gets tricky fast. Team leaders juggle different personalities. One driver gets stuck in traffic, another is out sick, and now the crew in the warehouse is grumbling about overtime. If you're the supervisor, you're right there in the middle, making quick calls. And don't forget about the customer. They want real-time updates, not excuses. In fact, a 2023 survey by ShipBob found that 47% of logistics customer complaints are about delayed or missing updates. That stat follows you around like a shadow.
People in logistics spend a huge part of their day solving these human puzzles. Here are a few challenges you might run into—and how folks in the field actually handle them:
- Clear Communication: Misunderstandings bring disasters. Good managers over-communicate—call, text, email, repeat.
- Expectation Management: Under-promise, over-deliver. A little honesty with the customer about timing saves headaches when things go sideways.
- Team Motivation: Small incentives and public shout-outs work. If the midnight shift just nailed a tough delivery, a pizza lunch goes a long way.
- Immediate Problem-Solving: Train your team to improvise. The best teams trust each other to fix things on the fly, without waiting for endless approvals.
Here's a quick look at just how much this people pressure drives the stress factor in logistics stress:
Source of Stress | % of Managers Citing It |
---|---|
Dealing with Customer Demands | 52% |
Managing Team Conflicts | 37% |
Lack of Communication | 33% |
So, working in logistics means you need to be a people person—fast with answers, good at calming nerves, and able to spin up solutions on the spot. If handling people under pressure isn't your thing, this part of the job will test you every single day.
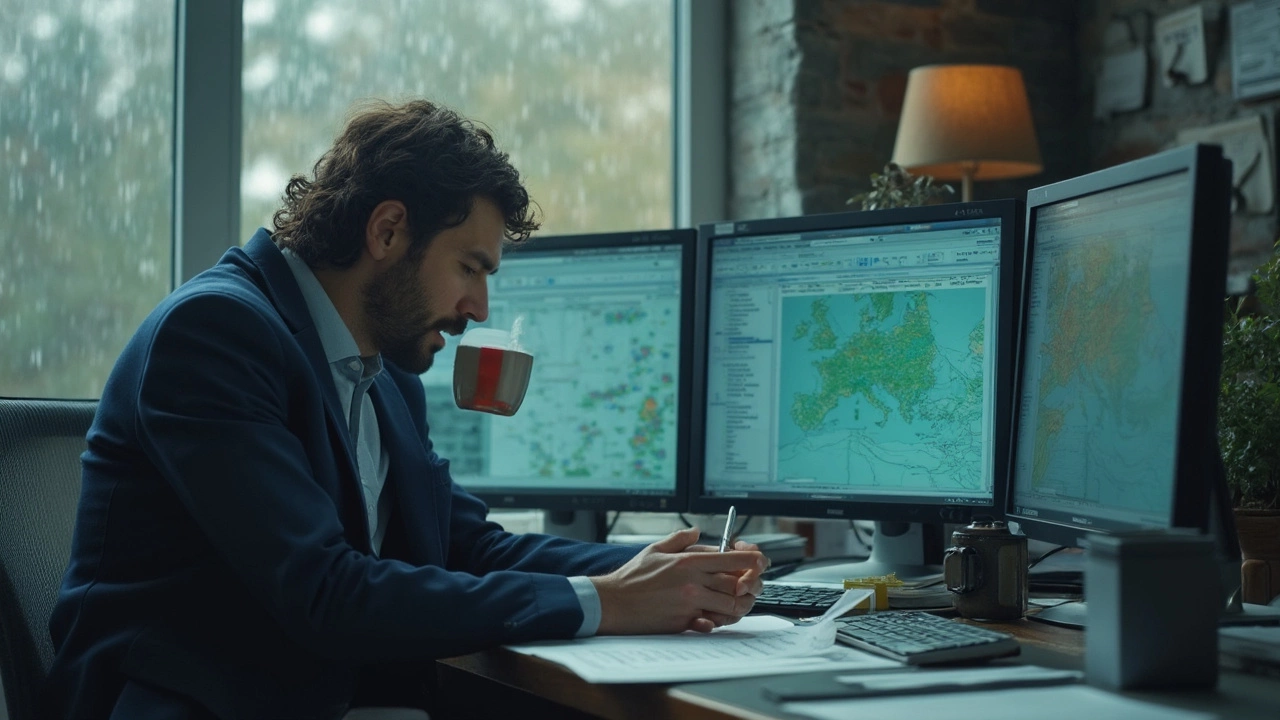
Technology Blues: More Gadgets, More Headaches?
Ask anyone working in logistics companies what’s changed their job the most, and technology will pop up right away. There’s warehouse management software, real-time tracking, robotics, and loads of apps that promise to “streamline” everything. Sounds awesome, right? But sometimes, all these gadgets make things feel even crazier.
Here’s the fact: while automation and digital tools do help get stuff from point A to point B faster, they also mean you’re never really disconnected. Notifications ping 24/7. If the software crashes or the system gets hacked, it’s chaos—shipments just sit there waiting for someone to fix it. Remember that big cyberattack in 2017 that shut down shipping giant Maersk? It cost over $200 million in losses. That’s the sort of nightmare that keeps logistics pros up at night.
Plus, every new system comes with a learning curve. Getting everyone trained up is a pain. And let’s be honest—sometimes you have five different programs and none of them talk to each other. You end up typing the same info in multiple places, which is exhausting and wastes time.
So, what can businesses do to keep tech stress low? A few things work:
- Pick software that’s user-friendly. Your team shouldn’t need a PhD to figure it out.
- Invest in regular tech training—not just for new hires, but for everyone.
- Back up data daily and have a plan for when software goes down.
- Don’t chase every shiny new tool. Focus on tech that truly solves your biggest headaches.
Here’s a quick look at how often tech trouble causes real slowdowns:
Type of Tech Fail | % of Logistics Companies Affected (2024 survey) |
---|---|
System Downtime | 64% |
Cybersecurity Issues | 38% |
Software Integration Problems | 53% |
One last heads up: even if gadgets make your job easier sometimes, you’ll still need to solve plenty of problems the old-fashioned way. Nothing beats a cool head and quick thinking, especially when the software decides it’s nap time right before your customer's big deadline.
How Industry Vets Tame the Stress
The best people in logistics companies don’t just grit their teeth and hope for calmer days—they use tried-and-true tricks to survive and even enjoy the chaos. Let’s get real about what works if you don’t want to burn out.
- Clear priorities every shift: Old-school pros don’t try to juggle everything at once. They pick the three most crucial jobs of the day and focus hard. This approach cuts the overwhelm and helps them track actual progress, not just busyness.
- Lean on smart tech: Paper logs? Hardly anyone uses them now. From route optimization apps to real-time inventory tracking, tech handles the repetitive stuff. A 2023 Transport Topics report even found that companies using automated tracking reported 35% fewer late shipments.
- Stay in the loop: Good communication stops things from falling apart. The seasoned crowd is big on group chats, daily huddles, and quick calls so everyone’s on the same page. No guessing, no drama.
- Respect the body’s limits: The old-timers swear by actual breaks—even if it's just 10 minutes at the warehouse wall with a coffee. Hydration, a quick snack, or stretching makes a real difference on a long shift.
- Keep perspective: Ever met someone in logistics who laughs off a massive pile-up? It’s not denial. It’s about seeing the bigger picture. They know not every setback is a disaster—tomorrow’s a new cycle, and problems can be solved.
Technique | Percent Using |
---|---|
Daily team check-ins | 64% |
Scheduling focused work blocks | 52% |
Tech-driven automation | 46% |
Short physical breaks | 41% |
If you ask an industry vet how they survive the logistics stress, many will mention one thing: don’t take it all home. For some, that means a strict no-emails-after-8pm rule; for others, it’s hitting the gym before their early shift starts. Marcus has his own rule: phone off at dinner unless it's a true emergency.
No strategy is perfect, but combining tech, smart routines, and downtime outside the job makes this wild ride less bumpy. And that’s the truth you don’t find in the onboarding manual.
Can Logistics Ever Be Chill? Balancing Work and Life
If you’re hoping for a totally laid-back gig in logistics companies, you might be dreaming. But that doesn’t mean work-life balance is impossible. Some companies are getting the message that all stress, all the time isn’t good for anyone. In 2023, a survey by the Bureau of Labor Statistics showed that about 70% of logistics managers reported moderate to high stress at work—but interestingly, the companies with flexible scheduling and reliable shift planning had lower reported burnout.
What really helps? Clear communication, backup systems, and knowing when to actually take a break (no checking emails while out with friends). Here are a few practical ways to manage life in a high-pressure logistics job:
- Set honest boundaries: It's easy to get sucked into always-on mode, especially during busy season. Let your team know when you are unplugged, and actually stick to it. If you fade out during family moments just to take a call, you’re headed for burnout.
- Use tech tools to your advantage: Workflow apps, shipment tracking dashboards, or automated alerts aren’t just cool tech—they're lifesavers for predictable days and decent sleep. Tech only adds stress when no one bothers to learn it or use it properly.
- Lean on your team: The best folks in logistics companies never try to fix everything solo. Delegating small stuff means you’ve got energy left for the big emergencies.
- Prioritize breaks like shipments: Even 15 minutes to walk outside can hit reset on your brain. Some major logistics firms actually set calendar reminders for everyone to take a breather, and it works—one large shipping company saw 20% fewer sick days after rolling out this practice in 2022.
- Flexibility counts: If your company offers different shift options or remote check-in, take advantage of it. It's not "lazy"—it’s survival.
If your employer isn’t helping out, it’s okay to be picky. Plenty of logistics companies are offering four-day workweeks or mandatory off-phone hours to attract talent. You don’t have to prove loyalty by sacrificing your sanity—it’s about results, not how many nights you’ve worked overtime.
Balancing work and life in logistics definitely takes effort. But using tech, setting real boundaries, and working for companies that respect your downtime can make it a lot less brutal. And once you find that groove? The stress doesn’t disappear, but it gets a whole lot easier to handle.