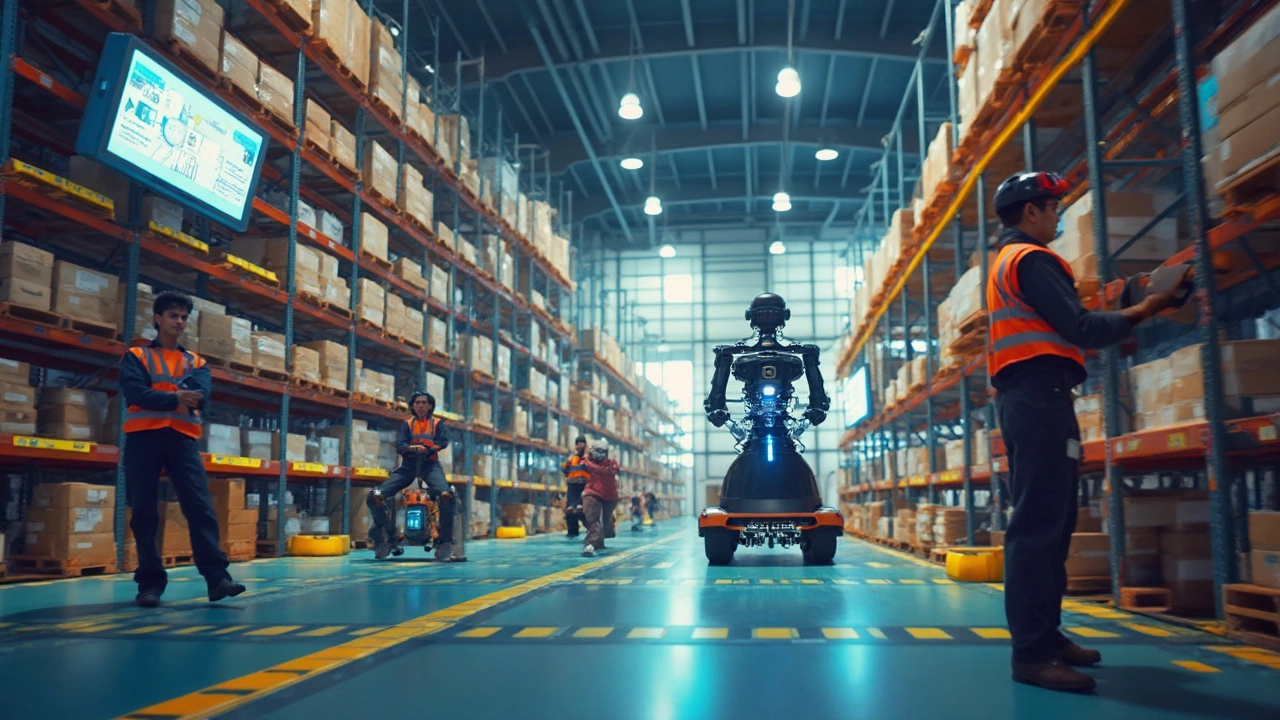
Waiting two days for a package can feel normal these days, but that wasn’t always the case. Amazon flipped the delivery game on its head, making fast shipping almost boringly predictable. The secret? It’s not just a sea of delivery vans or massive warehouses—it’s their insanely smart logistics software.
Here’s something cool: Amazon’s software maps where everything is in their warehouses, practically down to the millimeter. It knows exactly where that book or phone charger is on the shelf. And when you hit ‘Buy Now,’ the program springs into action—from picking to packing to giving drivers the fastest route—no guesswork, just pure efficiency.
- Amazon's Secret Sauce: Cutting-Edge Logistics Software
- Warehouses That Think for Themselves
- Delivering Faster with Data and Algorithms
- Lessons You Can Steal for Your Own Business
Amazon's Secret Sauce: Cutting-Edge Logistics Software
If you’ve ever wondered how Amazon logistics seems to know exactly what you ordered, where it is, and how fast it should be at your door, it all comes down to their advanced logistics software. This isn't the kind of off-the-shelf software regular companies buy. Amazon builds its own—connecting everything from your phone screen to a robot in a warehouse and then all the way to that smiley box at your doorstep.
One of Amazon’s big wins is their supply chain tracking. The company uses custom-built systems like Amazon Fulfillment Technologies, which lets them see real-time stock, track orders at every step, and predict when something will need to be reordered. This software keeps shelves full and cuts down on shipping delays. Fun fact: In a single day, Amazon’s software can process millions of transactions at once without breaking a sweat.
They also use something called “anticipatory shipping.” This is where their software actually predicts what you might order next based on your browsing and previous shopping. Sometimes, products end up close to you before you’ve even decided to buy them. Creepy or clever? You decide.
The magic doesn’t stop at tracking, either. Their warehouse automation system, powered by robots and tight orchestration with backend software, means a package can move through four stages—pick, pack, ship, and deliver—while you’re still figuring out what else to add to your cart.
Here’s a quote from Werner Vogels, Amazon CTO, in a 2023 interview:
"Software runs not just our website, but our entire logistics infrastructure. Every minor improvement in our logistics algorithms knocks seconds off the delivery process for millions of orders."
When you compare all these smart moves, it’s no mystery why a regular retailer struggles to keep up. Check out these stats showing how Amazon’s delivery speeds dominate:
Year | Avg. Delivery Time (Prime) | Competitor Avg. |
---|---|---|
2022 | 1.8 days | 4.2 days |
2023 | 1.6 days | 4.1 days |
Bottom line: Custom software and relentless optimization is what keeps Amazon’s logistics at the top of the game.
Warehouses That Think for Themselves
You’ve probably seen videos of those orange robots zipping around inside Amazon’s massive warehouses. These aren’t just for show. They’re Kiva robots, and they’re the heart of Amazon’s warehouse automation. Each robot gets real-time instructions from a centralized logistics software brain that tells it the fastest way to grab a shelf, bring it to a human packer, and get ready for the next task. This alone saves a ton of time—some reports show up to a 50% increase in picking efficiency compared to old-school warehouses.
But it’s not just the robots. Every item in an Amazon fulfillment center has a barcode and a specific spot, and the software tracks all of this constantly. If you decide to buy something, the system figures out which warehouse is closest to you and which route will be the quickest, so your stuff isn’t sitting around any longer than it needs to. That’s how they push so many goods in and out in a single day—during peak season, some fulfillment centers ship over a million packages a day.
Warehouse Fact | Details |
---|---|
Robots per warehouse | Up to 1,000+ |
Average time to pick an item | Less than 15 minutes |
Packages shipped per day (peak) | 1,000,000+ |
Another trick Amazon uses is random stow. Instead of putting the same item in one spot, identical products are stored all over the place. Sounds messy, right? But actually, the supply chain software handles this by telling workers (or robots) exactly where to find things, and this maximizes space and makes picking even faster. It’s just less walking and less wasted time.
If you run any sort of warehousing, even on a small scale, using smart tracking—barcodes, inventory software, and real-time location data—can cut mistakes and help you move stuff faster, just like Amazon does.
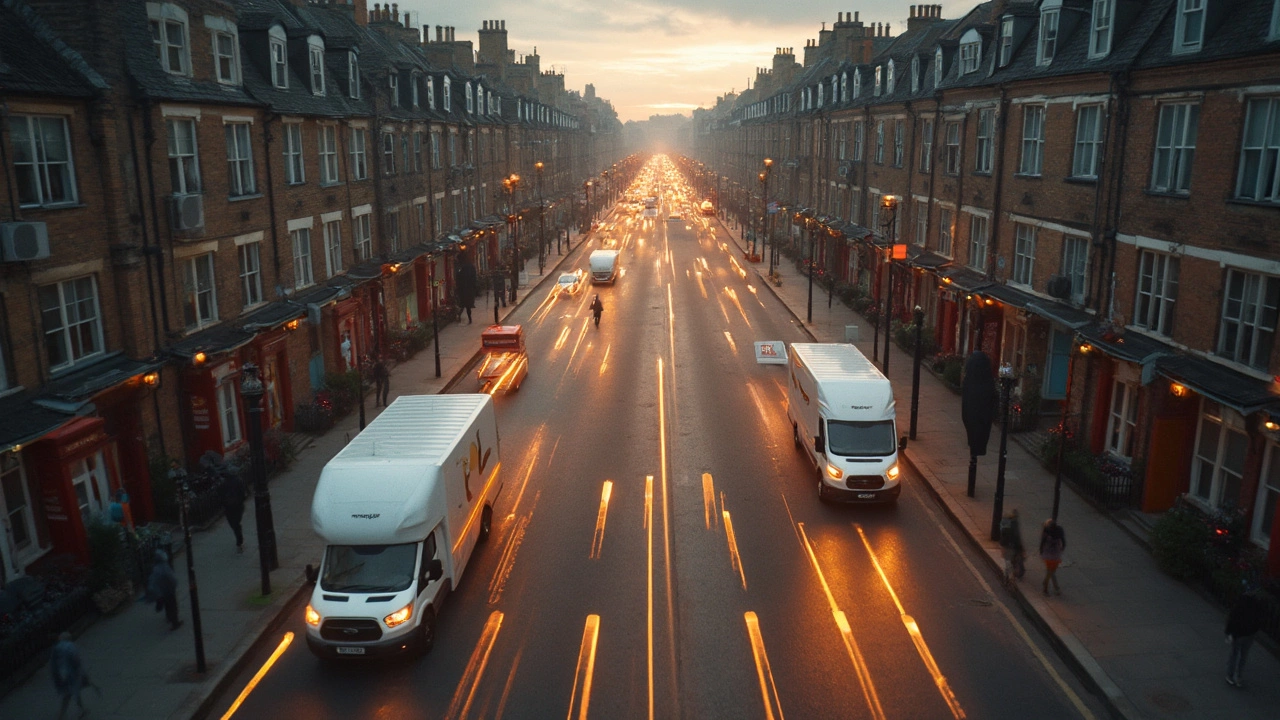
Delivering Faster with Data and Algorithms
This is where things get wild. Amazon logistics runs on data—gigantic mountains of it. Every box, truck, and package is tracked in real time. The company’s logistics software constantly chews through millions of transactions and location points to make fast decisions. It works out when to pick products, which workers should pack them, and even which truck your order should ride in. It’s all powered by algorithms, not hunches.
Take Prime Now, for example. If you order something for delivery within two hours, Amazon’s software doesn’t panic. It crunches data like local traffic, driver location, and warehouse activity to pick the perfect route. The system even lines up orders in the van so the driver can just step out and hand you the box—no rummaging, no wasted time.
And it’s not just about speed. Amazon uses predictive analytics to forecast when certain items will get hot. The software might stock up on umbrellas in your city days before a wet forecast hits. Less guessing, more delivering.
- Route optimization: The software picks smart paths, dodges traffic jams, and re-routes drivers if there’s an accident nearby. That’s how Amazon can squeeze in last-minute orders without breaking a sweat.
- Real-time tracking: Each package has a digital tag, and the system updates the package’s journey second by second. Not just for customers—managers see everything, so if something goes off track, they can jump in.
- Dynamic staffing: The software predicts busy times and calls in the right number of workers. If there’s a rush in one zip code, you get the staff to cover it. No one likes overtime, and Amazon’s tech makes sure it’s not needed unless things get wild.
Feature | How It Helps |
---|---|
Route Algorithms | Saves drivers up to 10 miles per route per day |
Real-Time Adjustments | Reduces late deliveries by 20% during peak seasons |
Predictive Demand | Cuts out-of-stock items in warehouses by nearly 35% |
Bottom line, without these data-driven tools and algorithms, Amazon’s fast delivery wouldn’t exist. If you’re eyeing faster shipping for your own business, pay attention to how tech can replace gut instinct with solid numbers. It’s a game-changer in the supply chain world.
Lessons You Can Steal for Your Own Business
You don’t need Amazon’s billions to improve your own logistics game, but you can definitely copy some of their best moves. Here’s what you can snatch from their playbook to get smoother operations, less wasted time, and happier customers.
- Automate Where You Can: Amazon uses robots and software for simple tasks like picking and sorting. If you’re not ready for robots, start small: barcode scanners and software can eliminate a ton of typing and manual mistakes. Even automating delivery status emails can save admin headaches.
- Track Everything—Seriously: Don’t rely on sticky notes or memory. Modern logistics software can track your stock in real time. When you know what you have and where it is, it’s way easier to stop running out or overordering.
- Route Optimization: Amazon’s delivery drivers don’t just guess the fastest route. Their software maps deliveries using smart algorithms that cut out wasteful detours. There are affordable apps that use similar math so your drivers make more stops in less time.
- Data Is Your Best Friend: Amazon is addicted to data. You can use data too—even simple stuff like which products sell fastest, or what’s always left on the shelves. A good supply chain dashboard turns guesses into facts.
Want a real-life example? According to a 2023 survey from Logistics Management, 67% of companies saw a drop in late deliveries after switching to cloud-based tracking tools. It’s not just Amazon—lots of businesses see big results from small tech upgrades.
Here’s a snapshot of some benefits small companies see after adopting basic logistics software:
Before | After |
---|---|
Manual inventory counting weekly | Live, always-accurate stock |
Drivers planning routes by hand | Automatic delivery route suggestions |
No tracking for orders | Customers get real-time tracking links |
So if slow shipments or mixed-up orders are driving you nuts, steal a few tricks from Amazon. A little technology can make a huge difference—even if you’re just running a small warehouse or a local delivery service.