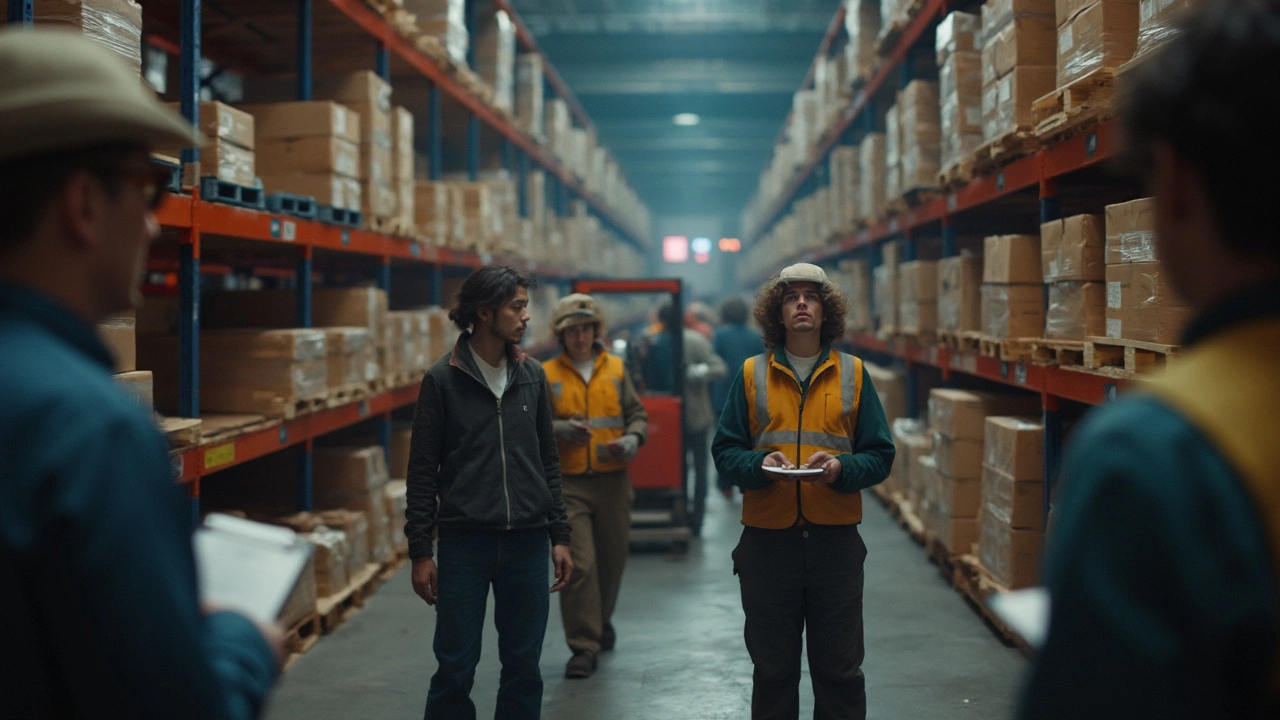
There’s this old myth that a warehouse manager just walks around with a clipboard, checking boxes and handing out orders. Anyone who’s actually done the job knows it’s more like juggling fire while riding a forklift. The pace barely lets up, especially when shipments run late or a delivery truck doesn’t show. If you’re thinking about stepping into this role, you need to know it can be both rewarding and overwhelming.
The number-one thing that stresses most managers? The constant pressure to keep things moving. Deadlines are real, and mistakes can mean big, expensive problems—like entire pallets going missing or angry customers chasing updates. And it’s not just about moving boxes. You’re dealing with staffing, sudden absences, safety issues, and sometimes, a broken loading dock at the worst possible moment.
- What Does a Warehouse Manager Really Do?
- Where Does the Stress Come From?
- How Do Warehouse Managers Handle Pressure?
- Tips for Managing the Tough Parts
What Does a Warehouse Manager Really Do?
The title "warehouse manager" sounds straightforward, but honestly, it covers a ton of ground. You’re not just one thing—think problem solver, people manager, planner, and sometimes, peacekeeper. At the most basic level, a warehouse manager runs the show when it comes to receiving, storing, and shipping goods. But let’s get into what that actually means day-to-day.
First, you’re responsible for making sure products get in and out of the building with almost no hiccups. That includes overseeing inventory, setting up schedules, keeping track of shipments, and catching mistakes before they snowball. If a certain order goes missing or a shipment is late, everyone looks to you for an answer—or, let’s be real, a miracle fix.
If you think a warehouse manager just delegates, that’s not really the case. You might need to train staff, handle onboarding, set safety standards, and sometimes fill in for someone not showing up. In a recent industry survey, 61% of warehouse managers said staff shortages happen at least once a month.
Here’s a quick look at the main duties you’ll juggle:
- Coordinating incoming and outgoing deliveries
- Managing and tracking inventory levels
- Scheduling shifts and moving people around as needed
- Overseeing health and safety to prevent accidents
- Resolving issues with stock, vendors, or employees
- Using warehouse management systems (WMS) and sometimes troubleshooting software that refuses to cooperate
Some larger operations even require you to handle budgets, run performance reports, and negotiate with shipping companies. In busy periods—like Black Friday or sudden supplier hiccups—you’ll find yourself pulled in a million directions.
Check out how the main responsibilities usually break down during a typical week:
Task | Average Weekly Hours |
---|---|
Supervising Staff | 15 |
Inventory Control | 10 |
Logistics & Scheduling | 8 |
Problem-solving | 5 |
Reporting/Admin | 4 |
Nobody really talks about how much multitasking is baked into this job. So if you’re looking at a warehouse manager position, be ready for fast pivots, quick decisions, and learning how to operate at full speed without dropping the ball.
Where Does the Stress Come From?
If you ask any warehouse manager what keeps them up at night, you’ll likely get a long list. The job isn’t just about running a smooth operation. It’s about handling a never-ending parade of surprises, and that’s where the stress really kicks in.
- Deadlines and Speed: Warehouses are all about speed. Shipments come and go, and if you miss a deadline, you risk losing business. That pressure never really lets up, especially in busy seasons.
- Staffing Issues: People call in sick. Someone quits without notice. Suddenly, you’re figuring out how to cover shifts with half your crew, and everything still needs to get out the door.
- Safety Concerns: The warehouse can be dangerous—forklifts zipping by, heavy boxes, and slippery floors. Managers need everyone to get home safe, so safety rules aren’t just for show. Mess up here and it can mean real injuries and tons of paperwork.
- Tech and Inventory Problems: Systems go down, scanners glitch, mistakes sneak into orders. That means double-checking everything, tracking lost items, and keeping inventory counts from turning into a nightmare.
- Customer Expectations: Nowadays, customers want everything fast, cheap, and perfect. If anything’s off—damaged goods, late shipments—they call, they email, and they want answers now.
According to a 2024 industry survey by Warehouse Insights, nearly 70% of US warehouse managers said that juggling conflicting demands from upper management and customers is their main cause of stress. That’s not just a number—it means a lot of folks are feeling squeezed from both ends, trying not to drop the ball.
The fast growth of online shopping hasn’t helped, either. A lot of companies now run 24/7 operations, and that constant hustle adds more pressure than ever before. Keep in mind, as e-commerce keeps booming, the job isn’t going to get calmer anytime soon.
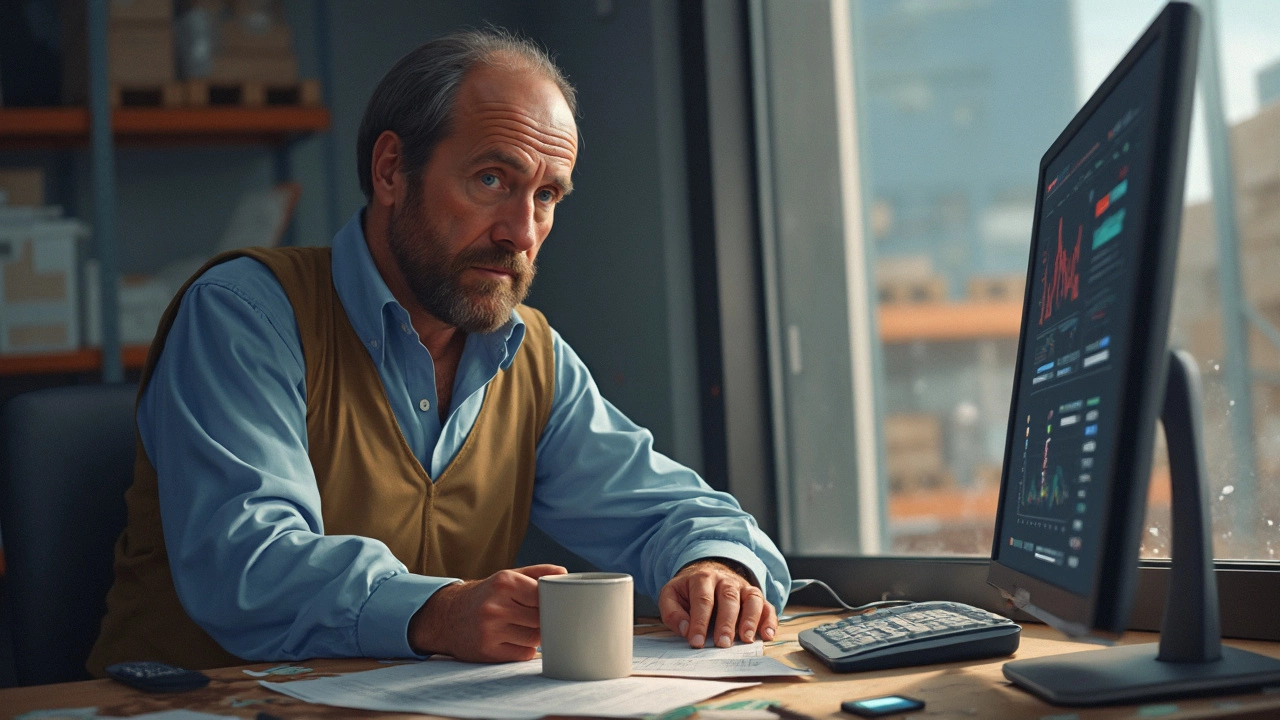
How Do Warehouse Managers Handle Pressure?
If you ask a warehouse manager how they deal with the stress, you’ll probably get a tired smile and a stack of survival tricks. It’s not about being superhuman—it’s about having proven routines and the nerve to act fast when things get messy.
The best managers swear by organization. Keeping track of tasks with software, whiteboards, or even color-coded sticky notes helps them not miss a beat. Smart tech, like warehouse management systems, makes tracking inventory and orders way easier. A 2024 survey by the Warehousing Education and Research Council found that 65% of warehouse managers use digital dashboards every day to keep chaos in check.
Staying cool also means not trying to do everything alone. Delegation is huge. Experienced managers trust team leads with small fires so they can focus on the real emergencies. They know that constant micromanaging is a one-way ticket to burnout.
Building solid relationships with the crew matters more than you’d think. When workers respect their manager, they’re more likely to step up without being asked. Some managers start every shift with a quick huddle, boosting teamwork and squashing confusion before it grows.
And honestly—taking short breaks isn’t optional. It’s standard practice for many managers to block out five minutes here and there to clear their heads. They use it to check in with themselves so the stress doesn’t pile up until it explodes.
- Use reliable digital systems for inventory and scheduling
- Delegate daily jobs and trust your team leads
- Hold regular crew check-ins to iron out confusion
- Block off small breaks, even on busy days
If you’re walking into a warehouse manager role, get ready for curveballs. But know that the pros survive by trusting their routines, using tech, and making sure they never carry the whole load alone.
Tips for Managing the Tough Parts
If you ask any longtime warehouse manager, they’ll tell you: the secret to surviving the stress isn’t working harder—it’s working smarter. You can’t control when a truck breaks down or someone calls in sick, but you can set up systems that make headaches less likely. Here’s what actually helps when the job gets tough.
- Master the art of delegation: Don’t try to do everything yourself. Train your team well and trust them to handle basic tasks. Give clear instructions, show them how to solve problems, and let them make small decisions without micro-managing.
- Lean on warehouse tech: Barcode scanners, warehouse management systems (WMS), and real-time tracking apps can save you hours each week. According to a 2024 survey by the International Warehouse Logistics Association, 79% of managers said their stress levels dropped after upgrading to a new WMS. Technology isn’t just fancy; it’s practical.
- Stay ahead with daily planning: Take 15 minutes before every shift to walk the warehouse, review schedules, and check incoming deliveries. This short routine makes it easier to spot problems early and avoid surprises during peak times.
- Keep communication tight: Use group texts, walkie-talkies, or shift meetings. Even five-minute huddles at the start of the day can help catch issues before they snowball.
- Put safety first, always: Nothing wrecks your day like an accident. Invest time in safety training and refreshers. It’s not just about compliance—it’s about keeping the team confident and productive.
Want a quick glance at what stress management can really do? Here’s a snapshot from a recent industry analysis:
Strategy | Reported Stress Drop (%) |
---|---|
Delegating tasks | 58% |
Upgrading tech | 79% |
Daily planning | 65% |
Improved communication | 61% |
Enhanced safety training | 42% |
If you keep these basics locked in, you’ll handle whatever chaos comes your way—and maybe even enjoy the rush.