
Ever heard someone say, "Just let the WMS handle it" and wondered what on earth they're talking about? WMS means Warehouse Management System. In plain English, it's software that helps people organize, track, and move stuff around in a warehouse. If you've ever lost a package, spent hours looking for products, or struggled with orders, you're going to want to know what a WMS can do.
Think of it as the brain of your warehouse. It tells you exactly where things are, when they're running out, and even who's picking and packing what. Instead of relying on spreadsheets or memory, everything is right there on your screen. No more wild goose chases or late-night panic when orders pile up.
- What Does WMS Stand For?
- How Does a Warehouse Management System Work?
- Key Features to Look For
- Benefits of Using a WMS
- Tips for Choosing the Right System
What Does WMS Stand For?
WMS stands for Warehouse Management System. It’s a fancy name for software that keeps track of everything going on inside a warehouse. Companies use a WMS to know what they have, where it’s stored, and how it's moving around. No more notebooks, no more guessing; with WMS, you see it all on a screen in real-time.
This technology isn’t new—big brands started using WMS back in the late 1970s. Back then, a WMS was mainly just digital inventory control. Now, it's snapped right into shipping, order picking, receiving, and even employee management. You can find it running in every industry, from fashion warehouses to pharma stockrooms and grocery mega-centers.
Here are some things a WMS handles behind the scenes:
- Tracks products as they enter and leave the building
- Shows you where every item is stored
- Helps plan the best routes for order pickers
- Connects with barcode scanners and RFID tags for accuracy
- Integrates with shipping systems to speed up deliveries
Check out this quick snapshot to see how many companies rely on WMS today:
Year | Global WMS Market Size (USD Billion) |
---|---|
2020 | 2.6 |
2023 | 3.1 |
2025 (projected) | 3.9 |
So, when someone talks about WMS, think of it as the command center for everything that moves in and out of a warehouse. It's all about making things faster, less stressful, and way more accurate.
How Does a Warehouse Management System Work?
A Warehouse Management System doesn’t just organize stuff—it actually follows every single product the moment it enters your warehouse until it leaves. The whole point is to keep things crystal clear so staff always know what’s in stock, where it is, and what needs to go out next. That’s why so many warehouses consider a good warehouse management setup the backbone of their operation.
Here’s how it usually works:
- Receiving: When new stock shows up, you scan barcodes or use RFID tags. The WMS logs every item and updates your inventory instantly.
- Putaway: The software literally tells you the best spot to stash each item so it’s easy to find later. No more guessing games.
- Picking: When an order comes in, the system shows staff exactly where to grab the items and often suggests the fastest route around the warehouse.
- Packing: Once items are picked, the WMS checks you’ve got the right stuff, then helps prep for shipping.
- Shipping: As packages leave, the system tracks them and even prints shipping labels. Your inventory numbers stay updated in real-time.
Modern WMS options use cloud tech so you can manage your warehouse from pretty much anywhere. That’s a lifesaver if you’re running more than one location. According to Tony Sciarrotta, executive director of the Reverse Logistics Association,
“You can’t manage what you can’t see. A WMS makes your whole warehouse visible and easy to track in ways that just weren’t possible before.”
Automating these steps cuts out the old paper-and-pen routines and slashes mistakes. Plus, most WMS tools can connect to other business systems, like accounting or online stores, so every part of your operation is in sync. That means fewer headaches and more time to actually grow your business.
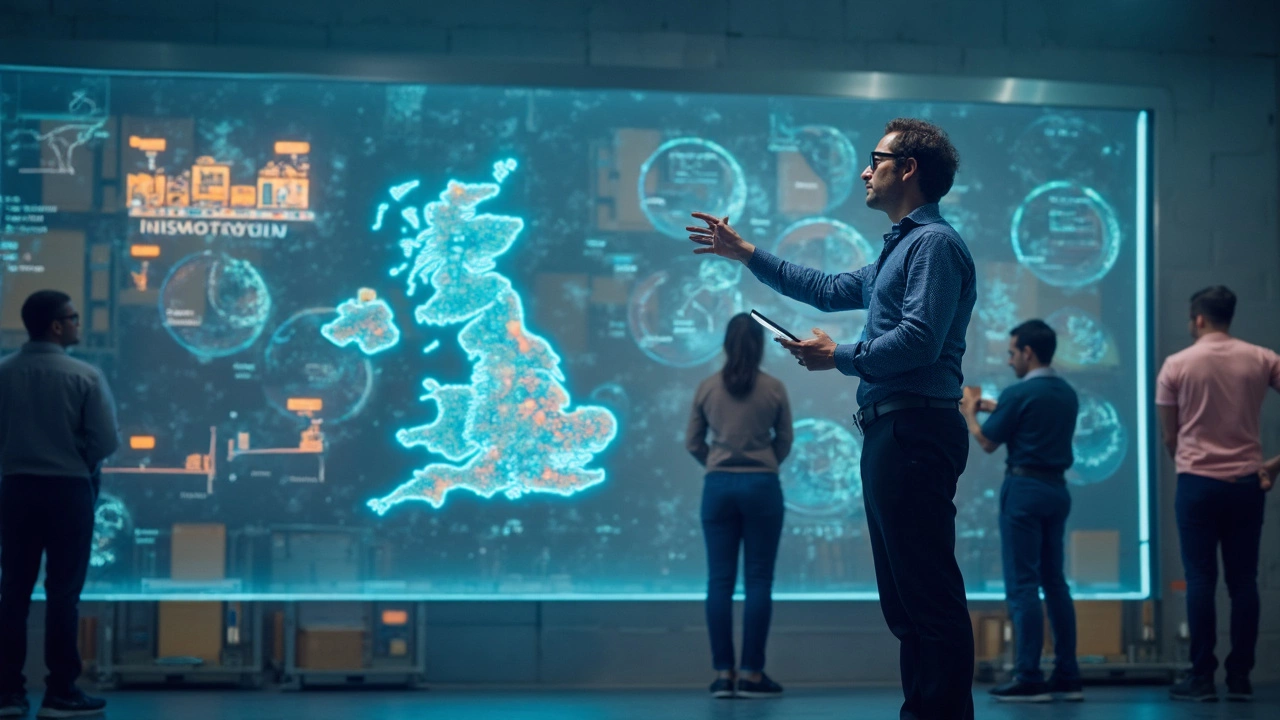
Key Features to Look For
If you're shopping for a WMS, don't settle for buzzwords or flashy dashboards. The right one will have tools that actually make warehouse life easier—no fluff.
- Real-Time Inventory Tracking: A must-have. You should be able to see exact stock levels every second, so you're never surprised by missing or overstocked items.
- Barcode Scanning: Ditch the pen and paper. Barcode scanners speed up picking and reduce mistakes. Check if the WMS works with your existing scanners or mobile devices.
- Order Picking Automation: Look for features that help with batch picking, wave picking, or zone picking. This cuts walking time and gets orders out the door quicker.
- Easy Integration: Whether you use Shopify, Amazon, QuickBooks, or custom ERP—your WMS should play nice with other tools. Good integration saves time and hassles.
- Reporting & Analytics: Don't just move boxes—understand your warehouse. Solid reports show you trends, bottlenecks, and opportunities to improve.
- User-Friendly Interface: If it takes a degree in rocket science to train new staff, forget it. You want clear menus, simple logins, and easy mobile access.
Here’s a quick look at some of the most-searched WMS features and their benefits:
Feature | Why It Matters |
---|---|
Real-Time Inventory | Avoids stockouts and overstocking |
Automated Picking | Saves hours per day on order fulfillment |
Integration | Keeps everything from accounting to shipping in sync |
Cycle Counting | Reduces the need for full physical inventory checks |
Cloud Access | Work from anywhere—great for teams on the move |
Don’t be shy about asking vendors for demos and testing how features work with your real warehouse data. If you find you’re constantly switching screens or numbers don’t add up, that’s a red flag.
Benefits of Using a WMS
Once you start using a WMS, you’ll wonder how you ever worked without it. The main perk is less chaos. Everything in the warehouse has a place, and the system tracks every move. No more hunting down missing products or double-shipping by mistake.
Speed is another biggie. With a warehouse management system, picking and packing isn’t left to guesswork. Workers get clear instructions—what to pick, where to find it, and the best order to do it. This cuts down on mistakes and means more packages go out the door faster. Some warehouses see order accuracy jump to over 99% with WMS in place.
Inventory counts get a big upgrade too. Instead of waiting for yearly stock checks and hoping the numbers add up, WMS keeps a real-time tally. This means you know instantly if you’re running low on something, helping you avoid running out or overstocking.
Ever dealt with returns? WMS makes it way easier to process returns, restock products, and keep track of what’s going back on shelves versus what goes out the door again. Plus, you get less paperwork—most things happen digitally, saving everyone time and headaches.
When it comes to company growth, a warehouse management system scales with you. Whether you handle 100 orders or 10,000, the process stays organized. It even helps with compliance needs, tracking batch numbers or serial codes for industries that require extra care.
- Reduces costly errors
- Saves time on training new staff
- Improves efficiency and speed of shipping
- Keeps inventory data up-to-date
- Supports smarter decision-making with good reports
Larger warehouses or companies with lots of moving parts often see a fast return on investment with WMS, mostly from fewer errors and better use of labor. If you’re dealing with product chaos or slow shipping, it’s probably time to think about a system like this.
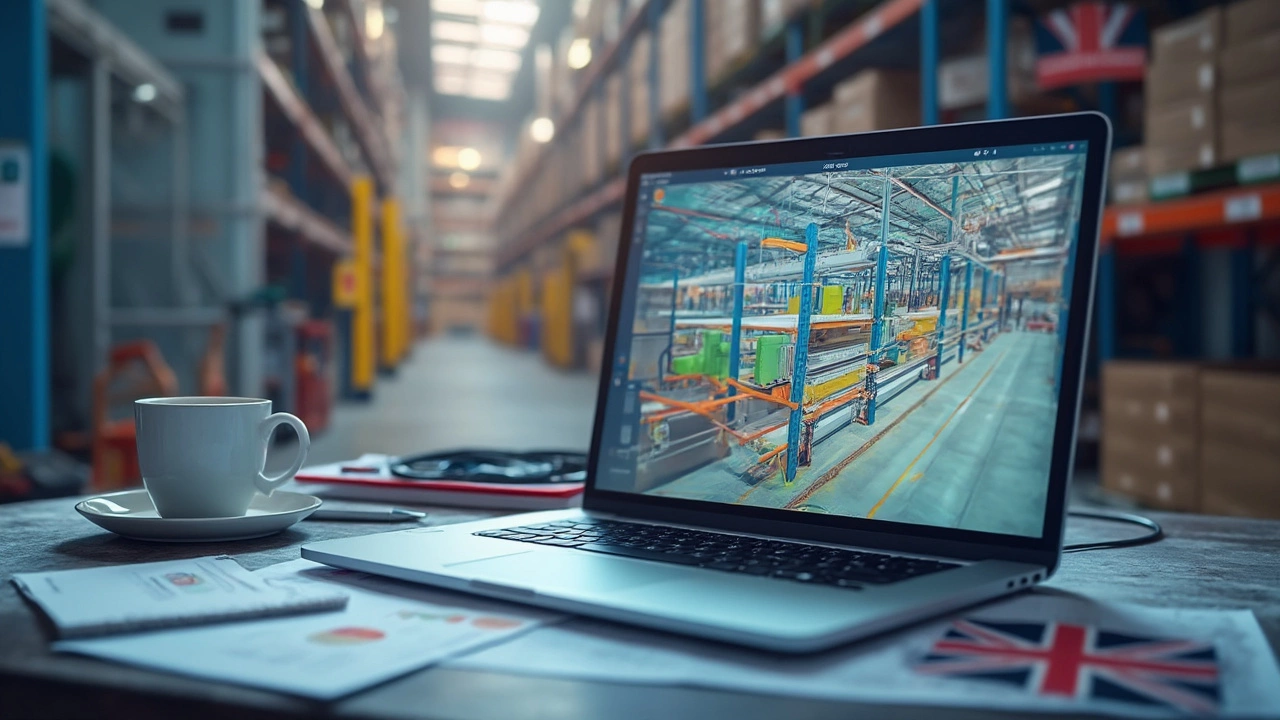
Tips for Choosing the Right System
There are a lot of Warehouse Management Systems out there. If you want a smooth upgrade, you’ve got to make sure the system actually fits your business—not just today, but a couple years down the road when things get busier. Here are some smart moves to make before signing up for a new WMS.
- WMS must connect with your current tools. Check if the system works with your inventory, shipping, and accounting software. If it doesn’t, you’ll spend too much time juggling between screens or copying info by hand.
- User-friendliness is key. If your team needs a two-week boot camp just to pick an order, it’s not the system for you. Ask for a demo and see how the process flows. The fewer clicks, the better.
- Think about mobile access. Lots of modern warehouses run on tablets and handhelds. Your system should work on those devices, so your team can log updates while on the move, not just from a desktop in the office.
- Scalability saves headaches later. Look for a system that can grow as your business grows—more products, more orders, maybe even more locations. You don’t want to start all over every time you reach a new milestone.
- Ask about support and updates. Even the best system hits snags. Make sure you have real people to call and that updates happen on a regular schedule.
Don’t forget to check reviews and ask other businesses in your industry about their experiences. They might point out things you’d never think to ask, like hidden fees or quirky setup steps. Some warehouse managers swear by scheduling a trial run, so you and your team can actually test processes live before making a commitment. That little bit of research now can save you a fortune in lost time and headaches later.