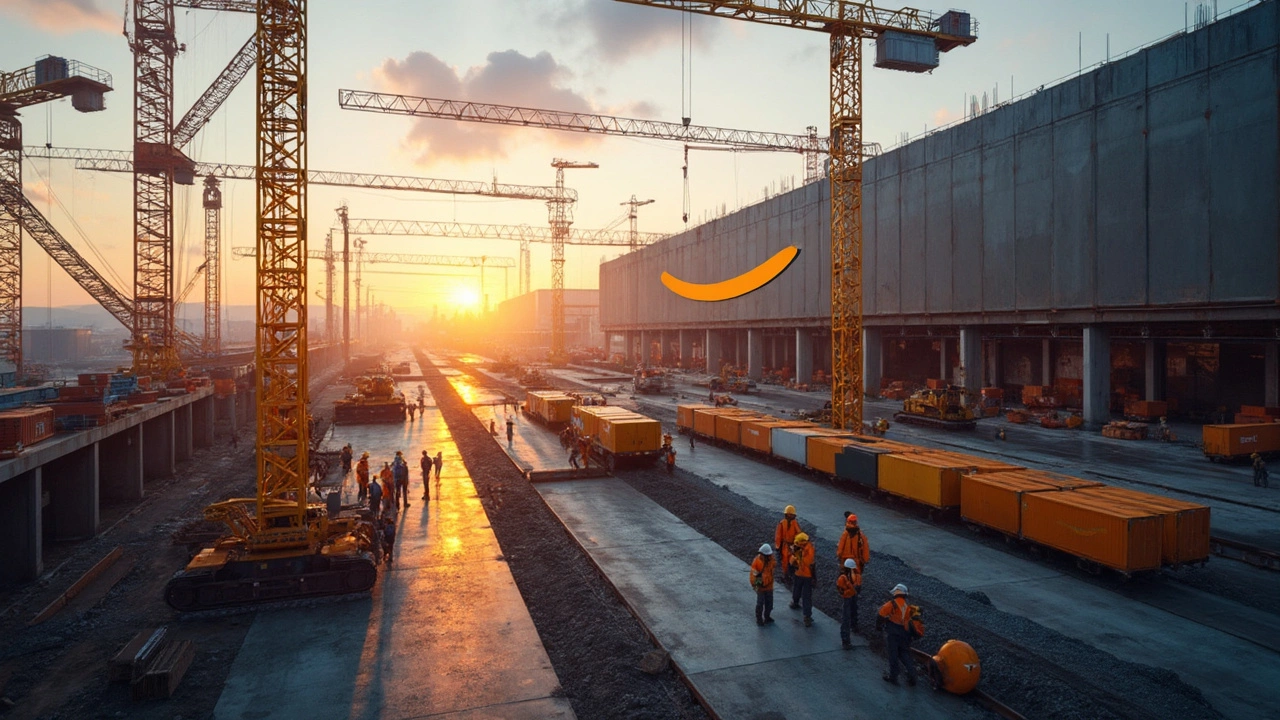
Drive past almost any major highway in the US, and there’s a good chance you’ll see a shiny new Amazon warehouse going up. But it’s not Amazon crews swinging the hammers or pouring the concrete—a handful of huge construction companies actually get it done. These projects come with serious budgets and wild deadlines, so the teams have to be some of the best in the business.
If you’re curious about how these operations run, here’s the scoop. Amazon hires general contractors like Clayco, Whiting-Turner, and ARCO—names you probably won’t see on everyday buildings, but in the industrial world, they’re basically celebrities. These companies have project managers, crews, and a deep bench of subcontractors who handle everything from steel framing to sophisticated robotics integration. And yes, there’s a lot more to it than just building big boxes—Amazon wants every inch to maximize speed and efficiency inside.
- The Big Players: Who’s Building the Warehouses?
- How Does the Building Process Work?
- What Makes Amazon’s Warehouses Unique?
- Tips for Bidding and Working on Amazon Projects
The Big Players: Who’s Building the Warehouses?
When it comes to building Amazon warehouses in the USA, Amazon always puts the job in trusted hands. The company doesn’t hire a random crew for these multi-million-dollar projects. Instead, it relies on a shortlist of major general contractors who can handle wild deadlines, massive scopes, and the complexity of robotic automation.
Let’s get specific. Clayco is a familiar name in the Amazon playbook, regularly managing projects well over a million square feet. Whiting-Turner’s teams have been spotted hustling on multiple Amazon facilities from coast to coast. Another big contender, ARCO National Construction, has built over 100 distribution centers for clients like Amazon, FedEx, and Walmart. Ryan Companies, Catamount Constructors, and Gray Construction are also regulars in this space.
Here’s why Amazon goes with these firms: they know how to manage big teams, juggle dozens of subcontractors, and deal with unexpected headaches (think supply delays or tricky permits) without missing a beat.
- Clayco: Led the 3.8-million-square-foot Wilmington, DE facility—one of Amazon’s largest on the East Coast.
- Whiting-Turner: Built multiple sortation and fulfillment centers, with recent projects in Texas and Florida.
- ARCO: Specialized in tilt-up concrete, making huge, rapid builds the norm.
- Ryan Companies: Known for high-tech builds that integrate Amazon’s robotics systems.
Amazon’s scale is wild. By early 2024, they had over 1,300 facilities in the USA—including fulfillment centers, sortation centers, and delivery stations. Each one is built from scratch, or retrofitted from an existing building, by these powerhouse construction teams.
Contractor | Avg. Project Size | Sample Amazon Projects |
---|---|---|
Clayco | 2,500,000+ sq ft | Wilmington, DE; North Little Rock, AR |
Whiting-Turner | 1,000,000+ sq ft | Houston, TX; Lakeland, FL |
ARCO | 900,000+ sq ft | Dallas, TX; Columbus, OH |
So, if you’re wondering who actually builds these logistical behemoths—look for these names on the jobsite vests. They’ve got experience, resources, and the track record to keep up with Amazon’s non-stop momentum.
How Does the Building Process Work?
Amazon doesn’t just pick a spot and start pouring concrete. The whole Amazon warehouses building process runs on precision and planning—and speed matters more than you’d think.
First up is site selection and prep. Amazon’s team scouts massive plots near major highways and cities, since location is everything for fast shipping. Once a deal is struck, the contractors come in to clear the land, level it, and test the soil. Any hiccups here can set the whole project back weeks.
Then it gets really intense. Construction starts with pouring huge foundations that can hold thousands of tons of goods and heavy machinery. Steel frames go up quickly, followed by roofing and the outer shell. The clock’s always ticking—Amazon sometimes sets deadlines as short as 10 months for a full warehouse build, which is lightning-fast for something this size. To pull this off, crews work long shifts, weekends, and even at night.
Next come the tricky insides. Crews install massive racking systems and conveyor belts, along with tech for robotics and scanners. Electrical and plumbing teams have to work right alongside concrete finishers and steelworkers. Everything has to support heavy automation and massive inventory.
- Special coordination meetings happen daily to avoid bottlenecks.
- Amazon has inspectors onsite almost every day to make sure no detail is skipped.
- If a problem pops up, there’s usually a small army of workers ready to double up shifts to keep on pace.
By the end of the build, another team swoops in to set up IT infrastructure—think Wi-Fi, security cameras, and control rooms. Finally, Amazon’s own engineers test out machinery before the doors ever open to employees. If you ever wondered why so many Amazon warehouses look the same, it’s not an accident—they use repeatable layouts to save time and money, letting contractors build the next one even faster.
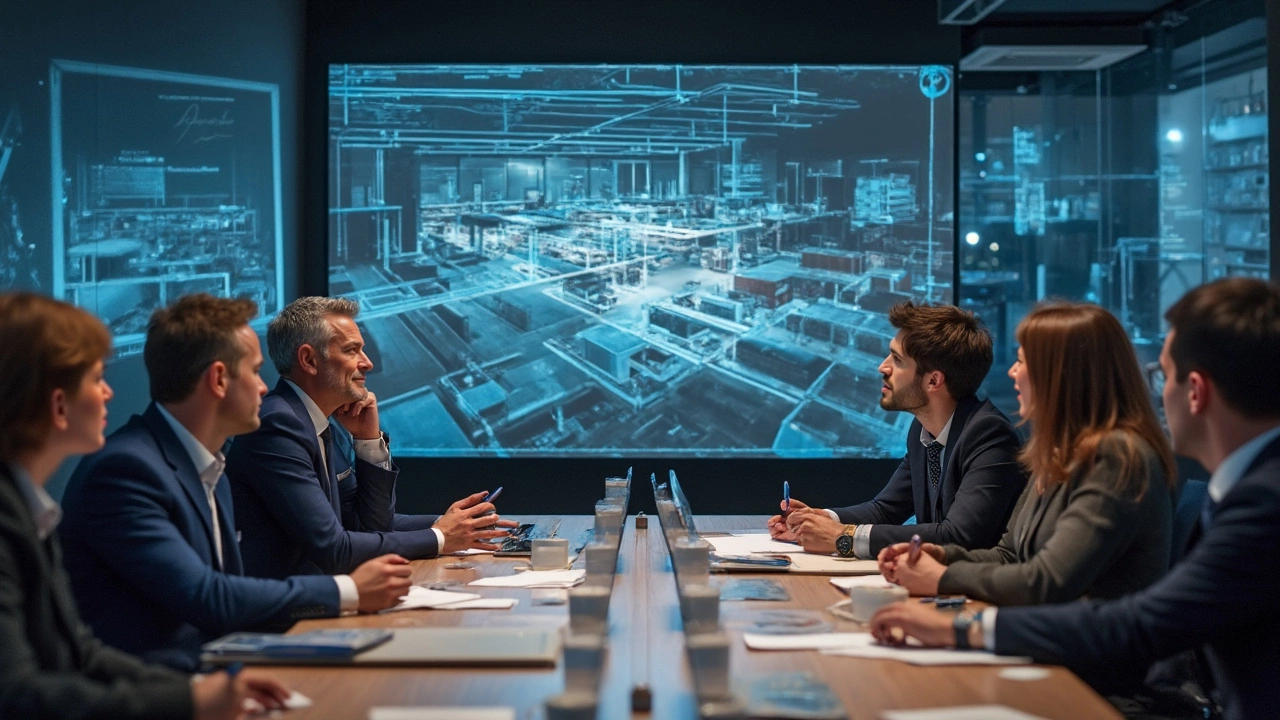
What Makes Amazon’s Warehouses Unique?
There’s warehouse construction, and then there’s building for Amazon. These places aren’t just storage—they’re where high-tech meets straight-up hustle. The blueprint for an Amazon warehouse looks completely different than what you’d find in a standard distribution center. Why? Because every square foot inside is designed to shave off seconds and boost how many packages get out the door each hour.
These warehouses—Amazon calls the biggest ones 'fulfillment centers'—often span over a million square feet. That’s like 15 football fields under one roof. Some even go up to four or five floors, stacked with conveyor belts, miles of shelving, and floors reinforced just to support fast-moving robots. More than 350 million items can move through a single location in a year.
The tech is wild. Robots zip around hauling products, guided by sensors and WiFi. QR codes mark paths. Employees—Amazon calls them 'associates'—work side-by-side with the bots, picking and packing. Every system connects back to Amazon’s software, so it all runs like clockwork. The climate control, LED lights, and fire systems are all up-sized, too, since these buildings run 24/7.
- Amazon warehouses often open less than a year after the first shovel hits the dirt. That’s crazy fast for buildings this big.
- They’re packed with advanced automation—drones, robots, and AI-driven software are common now.
- Every design tweak or construction method tested in one warehouse can get rolled out across dozens more, almost instantly.
- Even the parking lots are huge—some have to handle thousands of employee cars and a constant flow of semi-trucks.
Check out this quick data snapshot on a typical Amazon fulfillment center:
Feature | Amazon Fulfillment Center |
---|---|
Total Area | 1,000,000+ sq ft |
Construction Timeline | 9-12 months |
Robots per Warehouse | 2,000+ |
Employee Capacity | 1,500 - 3,000 |
Annual Package Volume | 350 million+ |
So, when you hear someone talking about a new Amazon project in their town, know it’s way more than just a regular warehouse popping up. It’s a tailor-made space for moving mountains of stuff fast, with tech and logistics that make even other big retailers look slow.
Tips for Bidding and Working on Amazon Projects
Landing a contract to build an Amazon warehouse isn’t your usual construction gig. Amazon is all about speed, scale, and sticking to strict guidelines. General contractors who win these jobs have usually handled giant industrial spaces before, and they can prove it with a track record. If you’re thinking about getting a foot in the door, here’s what matters most.
Amazon warehouses aren’t handed off to the lowest bidder—they’re built by companies with a proven system. Your bid needs a careful cost breakdown and a detailed timeline. Amazon reviews everything: safety records, past delivery speed, and even your tech know-how. Don’t forget: Amazon expects digital project management, up-to-the-minute progress reports, and absolute adherence to safety rules on the site.
"Amazon expects our partners to deliver large-scale projects on tight timelines while keeping quality high. Real-time data sharing and transparency are non-negotiable." — Claire Peters, Amazon Global Operations
Here’s what to keep in mind if you’re thinking about these projects:
- Get your paperwork right—Amazon’s prequalification covers finances, insurance, and previous project history.
- Use Building Information Modeling (BIM)—it’s the standard. If your team can’t use digital plans and progress updates, you’re already behind.
- Demonstrate expertise with tech—Amazon’s warehouses use robotics, automated conveyers, and smart systems. Subcontractors who understand these systems have a serious edge.
- Be ready for fast mobilization—Amazon builds can go up in under a year. Table below shows recent project timelines compared to averages.
Warehouse Name | Construction Time (Months) | Size (Sq. Ft.) |
---|---|---|
Joliet, IL | 13 | 1,000,000 |
Bessemer, AL | 11 | 855,000 |
Stockton, CA | 10 | 600,000 |
Industry Average (other retailers) | 16 | 800,000 |
And don’t sleep on safety. A single preventable accident can put your team on Amazon’s blacklist. Daily check-ins, safety huddles, and strict PPE enforcement are just the start—Amazon does random spot checks, and failing those means you’re done.
So if you want to work on these mega-sites, polish up your digital skills, get your safety culture sharp, and prove you can beat normal build timelines. That’s who wins with Amazon.