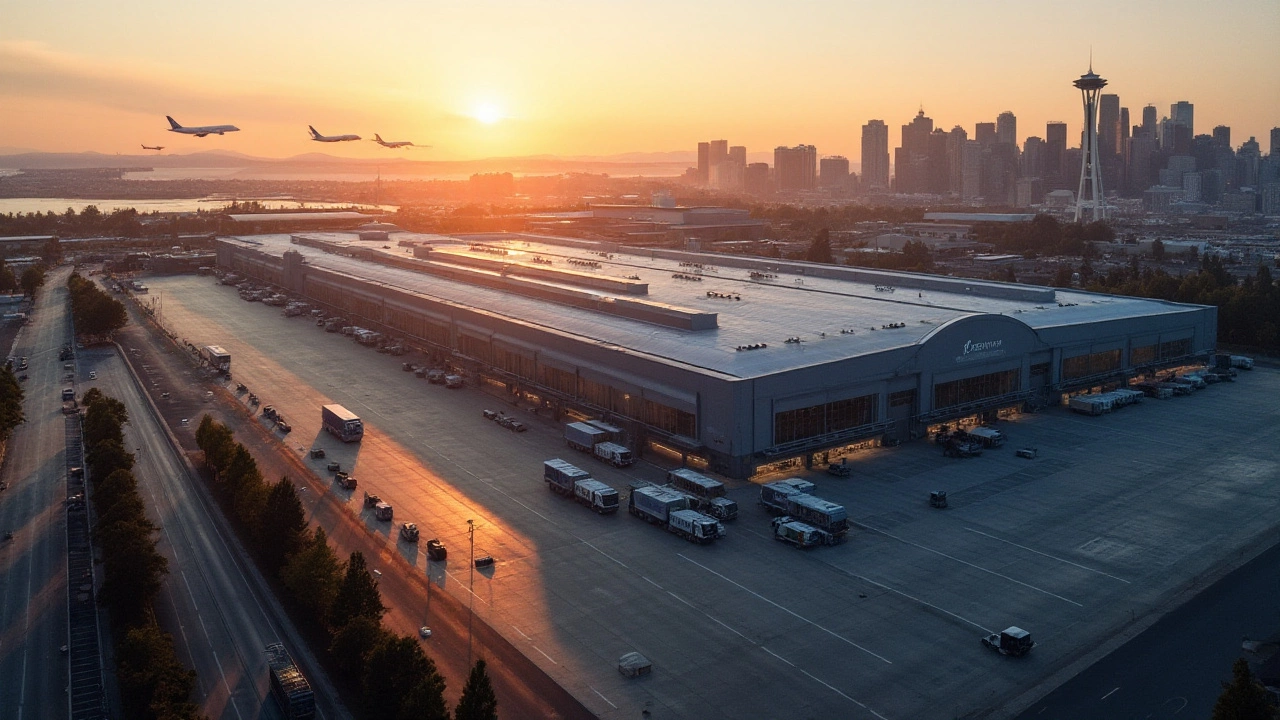
In the vast landscape of logistics and warehousing, the United States holds a monumental gem that sits atop as the largest warehouse – the Boeing Everett Factory. Nestled in Washington state, this colossal facility spans an astonishing 4.3 million square feet, earning its title by housing vast aviation components under its roof.
Exploring the depths of this warehouse unveils more than just its sheer size. It highlights the intricate dance between advanced logistics software and efficient warehousing systems. With cutting-edge technology at its core, it stands as a beacon of how automation and intelligent software redefine what’s possible in supply chain management.
Yet, the grandeur of such a facility brings its own set of operational challenges. Managing resources, optimizing space, and ensuring smooth logistics all demand innovative solutions. By understanding the adaptations and technological integrations within the Everett Factory, one can glimpse the future of warehouse management and its ripple effects across the industry. Join us as we navigate through this marvel, exploring its impact and setting the stage for new standards in logistics.
- The Giant of Warehouses
- Technological Influence on Logistics Software
- Operational Challenges and Solutions
- Impact on Industry Standards
The Giant of Warehouses
Tucked away in the heart of Washington, the Everett Factory by Boeing isn't just an extraordinary feat of engineering; it epitomizes what it means to be the largest warehouse in the United States. In terms of sheer scale, this colossal structure covers an incredible 4.3 million square feet, an area so vast that it could comfortably fit several sports stadiums under its roof. While the sheer size is an amazing element on its own, it's the facility's functionality and technological integration that truly make it a marveled giant in the realm of warehousing and logistics software.
Initially built in the 1960s to accommodate the construction of the Boeing 747, the facility has evolved to include the production of several other aircraft models, reflecting the dynamic needs of a shifting aerospace industry. Its design accommodates not just the enormous aircraft components, but also the cutting-edge logistics software that synchronizes these shifts in production. State-of-the-art automated systems and AI-driven logistics allow for unprecedented precision and efficiency, ensuring every part, no matter how small or large, arrives just in time for assembly. This is not just a warehouse; it is a marvel of modern logistics, setting benchmarks globally.
To truly grasp the enormity of this undertaking, it’s worth considering the people who keep such a facility operational. Thousands of employees work here, each one contributing a vital role in the daily dance of logistics that ensures efficiency and safety. The coordination of human efforts with advanced systems is akin to a symphony, where logistics software acts as the conductor.
As one Boeing executive once stated, "The secret to the Everett Factory’s success lies in its ability to adapt and integrate. Every day brings new challenges, and our team’s dedication to innovation keeps us moving forward." This quote underlines the philosophy that has driven the Everett Factory to not only be the largest but also among the most advanced warehouses of its kind.
The influence of the Everett Factory extends beyond its walls. Its prominence has inspired other sectors to rethink warehousing and manufacturing efficiency. By integrating advanced logistics software into their operations, companies worldwide strive to mimic the success they see in Everett, translating to enhanced productivity and minimized costs. This massive warehouse isn’t just storing airplane pieces; it's storing the future of logistics, one innovation at a time.
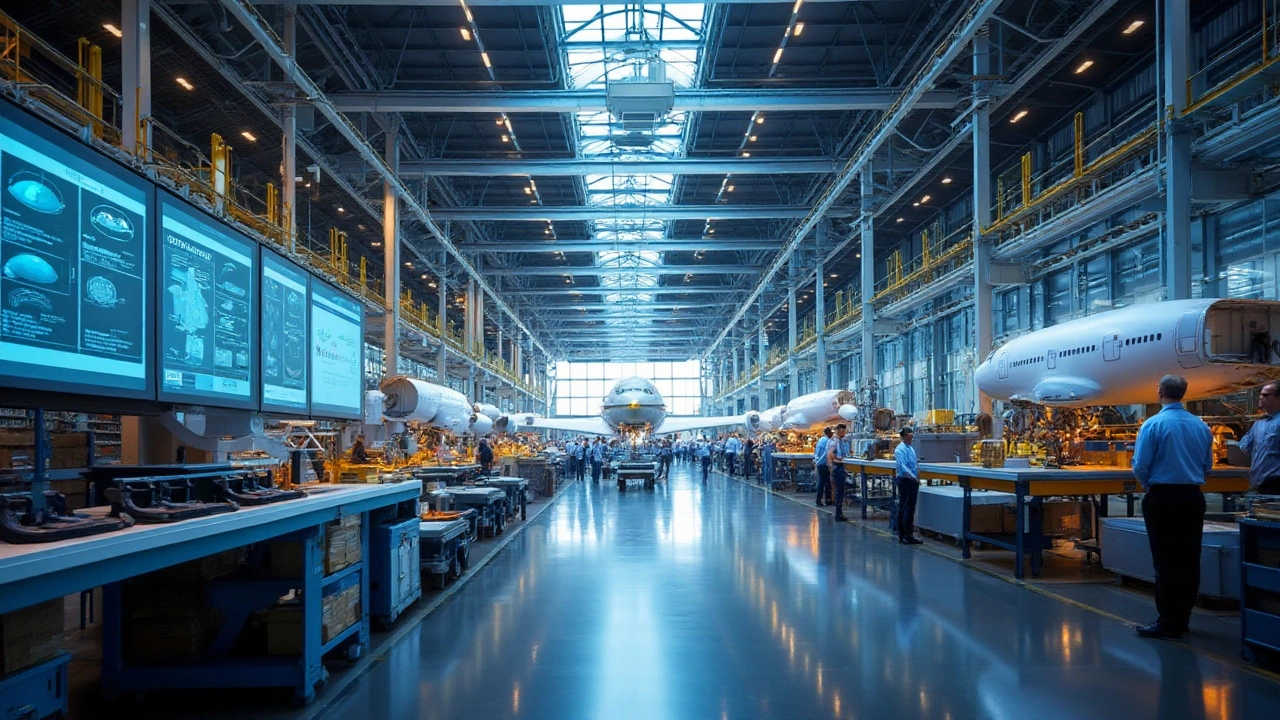
Technological Influence on Logistics Software
The Boeing Everett Factory is not merely the largest warehouse in the United States; it is also a hub of technological innovation that pushes the boundaries of logistics software. When we consider the largest warehouse in the US, we must also think about the technological solutions that enable its vast operations. The integration of sophisticated programs to manage inventory and logistics flows seamlessly is essential for a facility of this magnitude. These solutions harness the power of real-time data processing, tracking, and analytics to improve efficiency and reduce human error. As cargo cranes lift massive airplane components, they are monitored through sensors that communicate directly with management systems, synchronizing all aspects of logistics operations.
"Technology is not just a supporting tool but a core element of our logistics operations," says one expert from Boeing. "Our warehouse is built not just on physical space but on an intricate web of digital control."These systems offer numerous benefits, such as dynamic routing which optimizes delivery paths and adjusts them in real-time, thus saving fuel and time. Using GPS technology, logistics software can calculate the best routes for transporting components, an essential feature considering the size and scale of operations at Everett. Advanced machine learning algorithms contribute by forecasting demand accurately, adapting to fluctuations to minimize both surplus and shortage. Such technology not only arms businesses with the agility needed to meet rapidly changing demands but also facilitates sustainable practices by reducing waste.
Another facet of technological influence is seen in inventory management. The application of RFID (Radio Frequency Identification) tags in the warehouse management system has significantly transformed how inventory is tracked and managed. These tags provide precise information on every item's location, movement, and status in the supply chain. This advancement ensures that components required for aviation assembly are always at the right place and at the right time, fostering a just-in-time workflow that enhances productivity. Moreover, the integration of automated guided vehicles (AGVs) reduces labor costs and enhances safety by handling repetitive tasks that would otherwise require manual input.
Predictive Maintenance and Data Utilization
The predictive analytics capability of logistics software in such a titanic facility can never be overstated. Operating and maintaining a storage facility of this size requires proactive measures to prevent mechanical failures. With sensors embedded in machinery and infrastructure, any signs of wear and tear can be detected early. Predictive insights are drawn from data sets collected over time, enabling timely interventions and reducing costly downtime. The role of big data analytics is pivotal in deriving actionable insights from the vast amounts of information generated within the warehouse. This data facilitates better planning, supplier collaboration, and customer satisfaction by ensuring that Boeing remains nimble in its supply chain responses.Here's a snapshot of how technology enhances logistics:
- Real-time tracking and data analytics improve decision-making accuracy.
- Automation through AGVs increases operational efficiency.
- RFID and digital tools offer unprecedented inventory visibility.
- Machine learning aids in demand forecasting and adapting strategies accordingly.
In these ways and more, technological advancements at the Boeing Everett Factory offer a blueprint for how logistics software drives the evolution of modern logistics and supply chain management, setting a high standard for warehouses globally.

Operational Challenges and Solutions
Running the largest warehouse in the US, the Boeing Everett Factory, presents a unique array of operational challenges that demand innovative solutions. The sheer scale, with a footprint exceeding 98 acres under a single roof, requires meticulous planning and management to ensure the seamless assembly and distribution of aircraft components. One of the primary challenges is managing the massive influx and outflux of inventory, which includes everything from tiny bolts to massive airplane parts. To tackle this, the facility relies heavily on advanced logistics software, which tracks inventory in real-time, reducing errors and enhancing efficiency.
Maintaining temperature control and ensuring environmental protections for sensitive materials is another concern. Inside this vast space, maintaining consistent climate conditions is vital, not only for assembly precision but also to adhere to safety and regulatory standards. The integration of IoT technology within the warehouse enhances operational efficiency by providing real-time data analytics on temperature control, energy consumption, and machinery performance. This technology aids workers in making informed decisions to optimize operations continuously.
An additional layer of complexity arises from coordinating the workforce in such an immense venue. With thousands of employees operating across various shifts, communication systems and workflow optimization become critical. To enhance workforce efficiency, Boeing has invested in mobile platforms and wearable technology that allow for immediate information dissemination and task management. This implementation not only improves response times but also contributes to a safer working environment by minimizing potential communication bottlenecks.
According to TechRadar, "Technological integration in warehouses like Boeing's sets a benchmark for the entire logistics sector, proving that size is no hindrance when it comes to operational agility."
Addressing the challenge of space utilization, the Everett facility employs sophisticated algorithms to optimize the layout, ensuring every inch of the 4.3 million square feet is used effectively. These algorithms analyze spatial data and predict the best possible layout adjustments to maximize storage capabilities without hindering operational flow. Such advancements in warehouse management systems play a pivotal role in maintaining the Everett Factory's status as a leader in logistical excellence.
Given the immensity of the facility, transportation within the factory is another focal point. A network of automated guided vehicles (AGVs) operates alongside traditional human-driven equipment to facilitate the movement of materials across the warehouse. These AGVs are programmed to follow specific routes, reducing transportation time and labor costs while enhancing safety by preventing collisions and mishaps.
Incorporating renewable energy sources presents both a challenge and a solution. The vast roof area provides an opportunity for solar panels, contributing to the facility's sustainability goals and reducing energy costs. By embracing such green initiatives, Boeing not only cuts down on environmental impact but also sets a standard for massive industrial warehouses to follow.
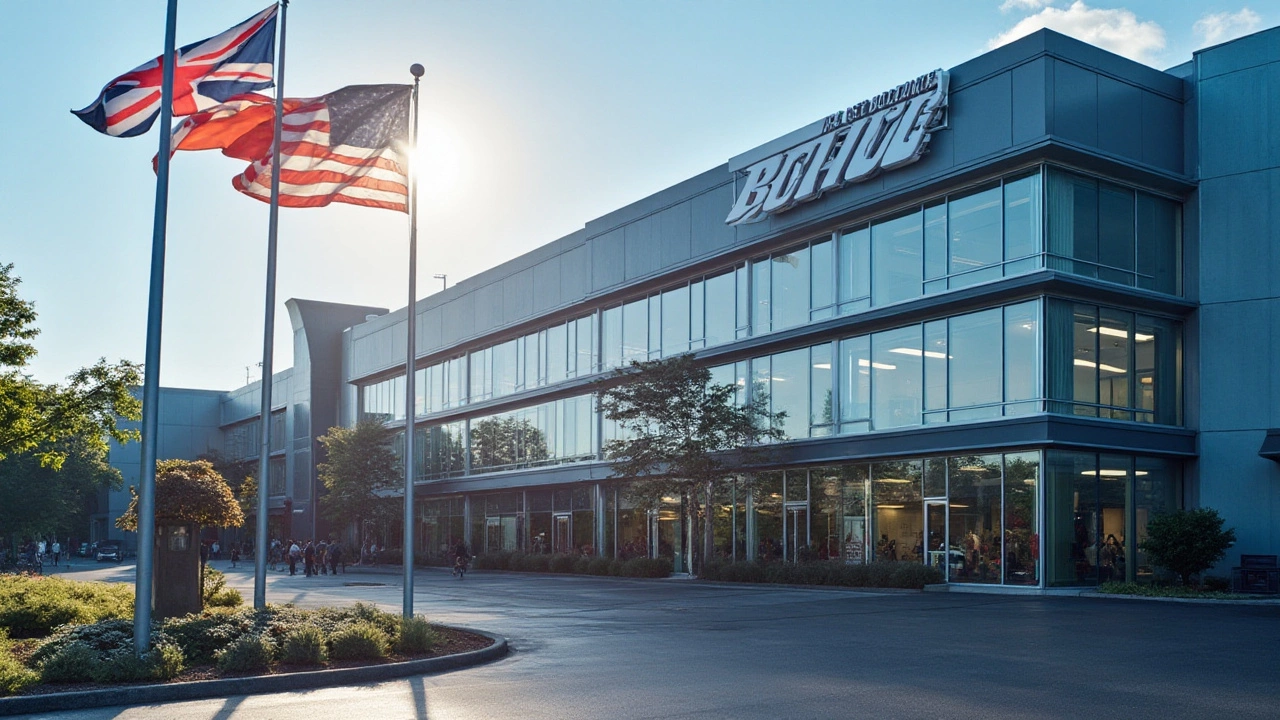
Impact on Industry Standards
The emergence of the Boeing Everett Factory as the largest warehouse in the US has fundamentally shifted industry standards, inspiring new benchmarks in both logistics and supply chain efficiency. An intricate interplay of size and technological prowess pushes other industry players to reconsider their operations. Where traditional warehousing once sufficed, the modern demands of the logistics world have spawned an era of advanced solutions and innovative practices.
This factory is not just about scale; it's a confluence of precision and optimization, where the magnitude is matched by the sophistication of its logistics software. The facility uses smart systems that integrate real-time data, transforming how inventory is tracked and managed across its vast expanse. These advancements have not merely elevated internal processes but set a precedent, promoting a paradigm shift across industries dependent on logistics.
Many organizations now view the sophistication and capabilities demonstrated by the Everett Factory as a template. For instance, deploying AI-driven logistics software has become more common, emulating the warehouse's ability to predict and mitigate supply chain disruptions proactively. Staying ahead in this field involves mimicking the layered integration of advanced technologies found at Boeing, setting a new norm across various sectors and prompting an industry-wide evolution toward digitalization.
The scale of operations at such a vast facility necessitates a dynamic balance between human capabilities and machine efficiency. As a result, warehousing roles are evolving, with an increasing emphasis on skilled labor familiar with emerging tech. As industries adapt to these changes, the focus shifts towards employee upskilling, ensuring workforce readiness to operate in these advanced environments. In a statement reflecting this trend, visionary analyst Jane Smith noted,
"Incorporating human-centric design into advanced warehouse operations is essential for sustainable growth."
The ripple effects from Boeing's endeavor extend beyond technology and workforce changes. The standard for operational sustainability has risen sharply within the logistics community. The warehouse industry, often criticized for its large carbon footprint, looks to the Everett Factory as a model, championing eco-friendly practices like energy-efficient systems and waste reduction. These strategies are increasingly becoming industry standards as companies aim to achieve their sustainability goals.
Moreover, the facility's influence is data-driven, extending right into industry analytics and decision-making frameworks. Advanced analytics gleaned from the warehouse’s operations offer indispensable insights that inform strategic planning for logistics stakeholders. As the insights circle back into the industry, businesses that maximize warehouse management benefits redefine industry standards and spearhead the shift towards a data-centric future.