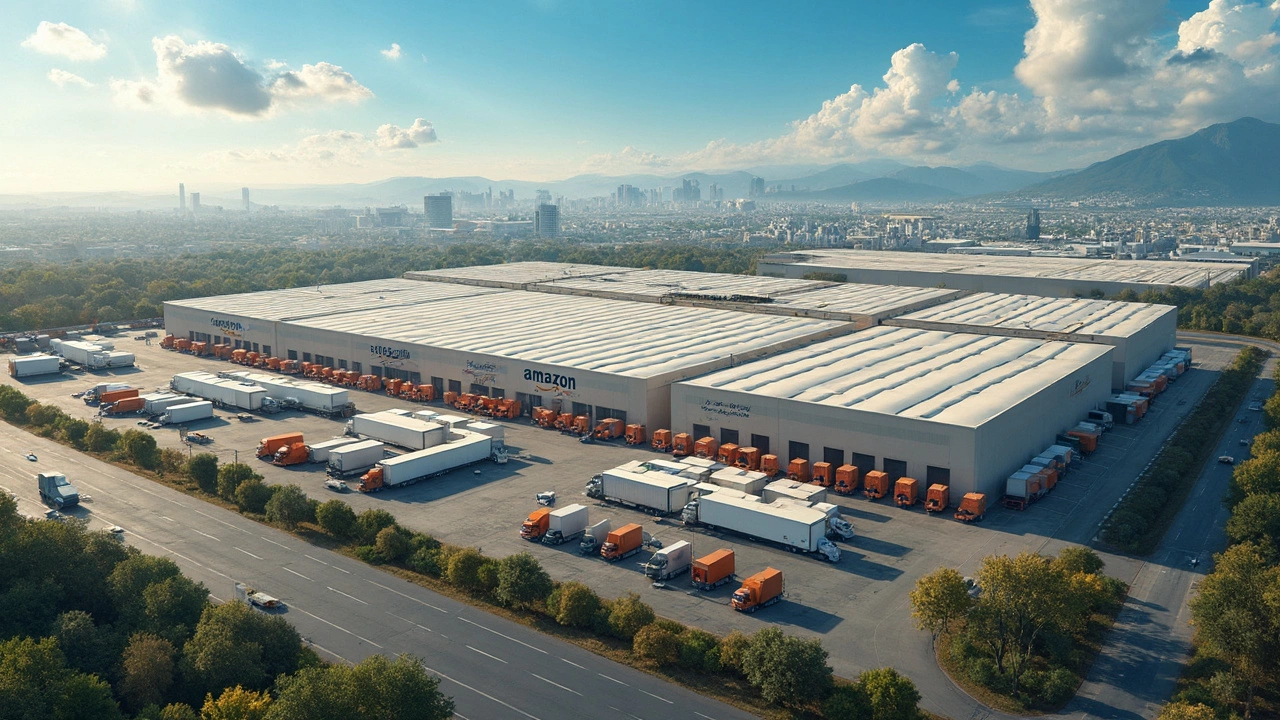
If you've ever wondered where all those Amazon packages are coming from, you're not alone. Amazon's warehouse network is a sprawling empire, strategically spread across various states to ensure we get our parcels as quickly as possible. So, which state boasts the most Amazon warehouses? It's a question with more than just a one-word answer, involving logistics, economics, and even geography.
For a few years now, California has been leading the pack, home to the most Amazon fulfillment centers. Why California? It's not just about size and population. California offers significant advantages: it's a giant consumer market and has access to essential ports for imports. Plus, the state's infrastructure supports the high-speed delivery demands that Amazon is known for.
- Amazon's Warehouse Empire
- Leading State by Numbers
- Factors Influencing Location Choice
- Economic Impact and Benefits
- Future Trends in Warehousing
Amazon's Warehouse Empire
Amazon's warehouse network, often referred to as its logistics backbone, is nothing short of massive. Over the years, this retail giant has multiplied its warehouse presence all over the United States, allowing it to fulfill the promise of lightning-fast delivery. But what's going on behind the scenes that enables such swift fulfillment?
The core of Amazon's logistics magic is its strategic placement of Amazon warehouses, also known as fulfillment centers. These warehouses are crucial to their operations, acting as the places where items are stored, sorted, and packed for delivery. With hundreds of warehouses across the U.S., they are positioned to reach a significant majority of the population within just a few hours.
Strategic Location Choices
Amazon doesn't plant these warehouses just anywhere. The company carefully selects locations based on several factors, including proximity to major urban areas, transportation infrastructure, and even state tax incentives. These choices ensure that products can be delivered quickly and cost-effectively.
The Sheer Scale
Numbers can truly paint the picture. As of the latest counts, Amazon boasts over 110 active fulfillment centers, each varying in size and capacity. Some of the biggest can cover hundreds of thousands of square feet, comparable in size to dozens of football fields.
State | Number of Warehouses |
---|---|
California | 40 |
Texas | 35 |
Illinois | 28 |
With California leading the list, its combination of market size and logistics infrastructure makes it a hotbed for warehouse solutions. Texas and Illinois also show strong presence, driven by their central locations and statewide advantages in logistics management.
Amazon's warehouse strategy isn't just about getting packages out faster; it's also about keeping costs down. Each fulfillment center reduces the distance a package has to travel, allowing Amazon to optimize shipping expenditures. By shipping from a nearby location, Amazon cuts down on shipping times, fulfilling their Prime delivery promises.
Leading State by Numbers
As of 2025, California is the reigning champ when it comes to the number of Amazon warehouses, making it a key player in Amazon's logistical strategy. This massive state hosts over 35 Amazon warehouses, including both fulfillment and sortation centers. The sheer number gives California a significant edge in the warehouse solutions game, allowing for quick delivery times to millions of customers.
Why does California take the lead? Well, it boils down to a few crucial factors. First off, California’s vast population and consumer base make it a vital hub. It also boasts one of the strongest infrastructures of any state, with efficient transportation networks that are vital for distributing goods rapidly and effectively. Plus, being home to vital ports like Los Angeles and Long Beach aids in handling international imports, keeping those Amazon shelves stocked.
It's not just about constraints, though. Consider revenue potential. A large portion of Amazon’s sales comes from California cities, making it economically strategic to maintain a heavy presence there. And, let’s not forget labor—California provides Amazon with a substantial workforce to handle operations smoothly.
Breaking Down the Numbers
Here's a quick snapshot of Amazon’s footprint:
Location | Number of Warehouses |
---|---|
Los Angeles Area | 15 |
San Francisco Bay Area | 7 |
Inland Empire | 13 |
This table highlights how these logistics nodes are not arbitrarily placed but are instead positioned near the largest urban centers to maximize efficiency and minimize delivery times.
Ultimately, the concentration of Amazon warehouses in California illustrates how strategic logistics can power a retail giant. It also sets the stage for how other states might adapt to attract similar warehouse investments in the future of warehousing.
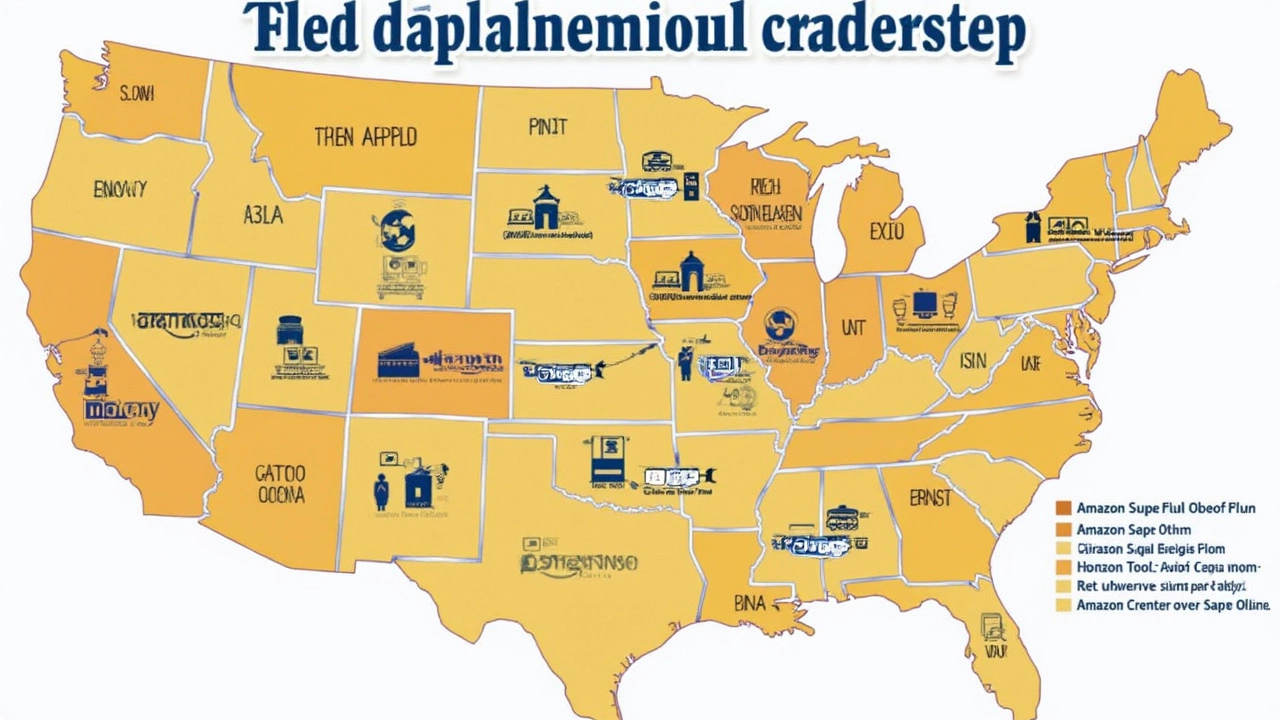
Factors Influencing Location Choice
Amazon doesn't just pin a map and throw a dart to pick its warehouse locations. There’s a method to the madness, and a few key factors play major roles.
1. Proximity to Major Markets
Being close to large consumer bases reduces delivery times and costs, which is crucial for services like Prime's two-day delivery promise. States with big cities or high population densities naturally attract more warehouses.
2. Transportation Infrastructure
Efficient transport networks, including highways, railroads, and airports, are essential. The easier it is to move goods in and out, the better it is for Amazon's logistics. Access to these infrastructures can make or break a site choice.
3. Economic Incentives
Some states offer tax breaks or other financial incentives to attract big players like Amazon. These perks can tip the scales in favor of one location over another.
4. Workforce Availability
A robust local labor market is crucial. Warehouses need workers, so places with higher unemployment rates might be more appealing due to the availability of willing and ready workers.
5. Real Estate Costs
Land prices and lease agreements can significantly impact the bottom line. States where real estate is relatively cheaper can be more attractive, allowing Amazon to build bigger and more efficient facilities.
Amazon juggles these factors to optimize its warehouse distribution strategy, always aiming to improve efficiency, reduce costs, and speed up delivery times. So next time you see an Amazon van in your neighborhood, you’ll know a bit more about the logistical magic behind it!
Economic Impact and Benefits
When Amazon sets up shop with its warehouses in a state, it’s like rolling out a red carpet for local economies. California, with its plethora of Amazon fulfillment centers, is a prime example of the ripple effects on job markets and regional development. Let’s break it down.
Job Creation
One of the most immediate benefits of having Amazon warehouses is the boost in employment. Each facility generally needs around a thousand workers. This isn't just about picking and packing; there are positions in management, maintenance, logistics, and more. For states with higher unemployment rates, these jobs can be a game-changer.
Infrastructure and Local Business
When you have a giant like Amazon in town, the infrastructure often gets an upgrade. Improvements in roads, transportation, and utilities can follow as a natural progression. Plus, local businesses, especially shipping companies and suppliers, tend to see increased demand. It's a win-win.
Tax Revenue
Local governments often benefit from increased tax revenue. While Amazon and many states negotiate tax incentives, the influx of new employees and business inevitably boosts state tax income. This can then be redirected to improve schools, roads, and public services.
Economic Benefits |
---|
Job Creation |
Improved Infrastructure |
Increased Tax Revenue |
To sum it up, the presence of Amazon warehouses doesn't just mean faster delivery for eager shoppers. Its impact layers through job markets, infrastructure improvements, and even local tax dynamics, making it a significant player in economic growth wherever it establishes operations.
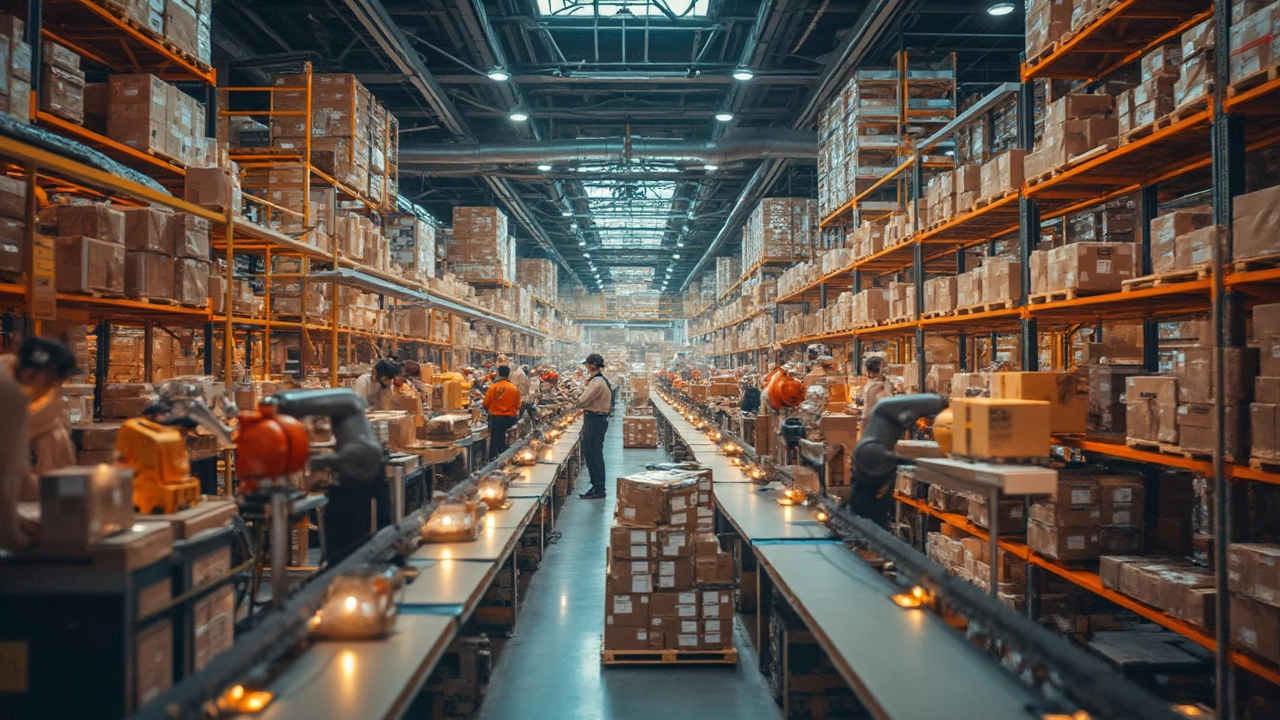
Future Trends in Warehousing
Warehousing is changing fast, and keeping an eye on future trends is crucial. With the continued growth of e-commerce and the demand for faster deliveries, businesses are being pushed to rethink their logistics strategies.
Automation and Robotics
One of the most significant trends is the rise of automation and robotics in Amazon warehouses. Robots are increasingly used for tasks like sorting and transporting goods, making the processes faster and more efficient. This doesn't mean robots are replacing humans entirely, but they are making warehouse jobs less physically demanding. The bonus? Faster operations mean your orders might arrive even quicker than they do now!
Green Warehousing
Another trend is the push for sustainable practices. Green warehousing is becoming more popular, with companies looking to reduce their carbon footprints. This can mean anything from using solar panels on roofs to optimizing delivery routes to save on fuel. These efforts not only help the environment but also can reduce operation costs in the long run.
Urban Warehousing
As cities grow, so does the concept of urban warehousing. This trend involves placing fulfillment centers closer to city centers to reduce delivery times. Consumers love getting their packages in hours rather than days, and urban warehouses are key to making this happen. Of course, it involves dealing with higher real estate prices and zoning regulations, but the payoff is worth it.
Year | Estimated Increase in Automation Use |
---|---|
2025 | 30% |
2030 | 50% |
Overall, the future of warehousing is exciting. As technology advances, we'll likely see more innovations that keep improving how products are stored and shipped. One thing's for sure: warehouse solutions will continue evolving to meet our ever-increasing expectations for speed and sustainability.